What is Friction Loss in a Pipeline?
Friction loss in a pipeline refers to the loss of pressure that occurs as fluid flows through a pipe. This pressure loss happens due to the resistance created by the friction between the fluid and the pipe walls, as well as the friction between the fluid particles themselves. Understanding and managing friction loss is essential for engineers looking to design efficient pumping and piping systems.
Analogy: Crowds Exiting a Football Stadium
Imagine a crowded football stadium where everyone is trying to leave after a big game. The stadium has multiple exits, but the passageways are narrow. As thousands of people move through these tight spaces, they slow down, creating a bottleneck. The movement of people becomes sluggish, and it takes much longer to exit the stadium than it would if the passages were wider and less congested.
This scenario is similar to how friction loss works in a pipeline. When fluid flows through a narrow pipe, it encounters resistance, much like the crowd in the stadium. The smaller the pipe diameter, the greater the resistance, causing the fluid (like the people) to move more slowly. Just as wider passages would allow the crowd to exit more quickly, choosing a larger pipe diameter can reduce friction loss and allow fluid to flow more efficiently.
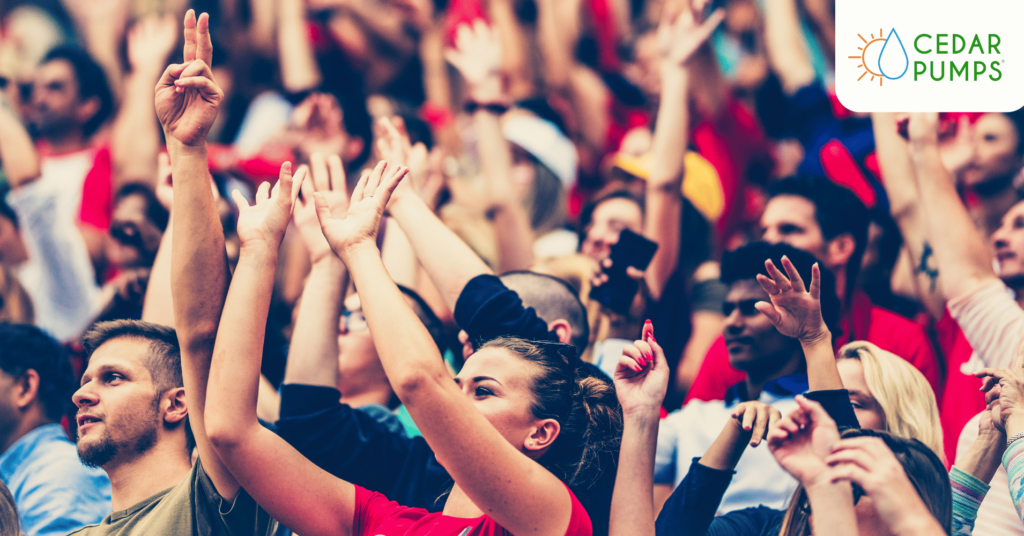
Factors Affecting Friction Loss in Pipelines
Several key factors influence friction loss in pipelines:
- Pipe Material and Roughness: Pipes with rough surfaces cause more friction, leading to higher pressure loss. Choosing smoother pipe materials can reduce friction loss.
- Fluid Velocity: Faster-moving fluids encounter more friction, which increases friction loss. Controlling fluid velocity is crucial for efficient system design.
- Fluid Viscosity: Thicker fluids, with higher viscosity, have more internal friction. This results in greater friction loss as they move through the pipeline.
- Pipe Diameter: Smaller pipe diameters create higher friction loss because the fluid has less space to move through, increasing resistance. Selecting the appropriate pipe diameter is vital to minimize pressure loss.
Understanding these factors allows engineers to make informed decisions when designing piping systems, ensuring optimal performance and efficiency.
Optimising Pump Performance with Cedar Pumps Online Sizing Tool
If you’ve used the Cedar Pumps sizing app, you might have noticed that it sometimes limits the pump options available for certain design parameters. This is particularly evident when pumping fluid over long distances through a small diameter pipeline. As more panels or restrictions are added to the system, the friction increases, leading to inefficient power use and less profitable outcomes for the end user.
Our app is designed to automatically detect scenarios where friction loss could impact efficiency. It then presents the most economical options to achieve the desired yield, while excluding less efficient choices. For instance, adjusting the pipe diameter in the app can significantly impact the friction loss calculations, helping you optimise your system for better performance.
Best Practices for Minimising Friction Loss
To reduce friction loss and enhance system efficiency, it’s important to follow best practices:
- Avoid Reducing Pipeline Diameter: Ensure that the pipeline diameter is not smaller than the pump outlet size. This helps to minimize resistance and improve overall system performance.
- Regularly Review System Design: Use tools like the Cedar Pumps sizing app to assess and adjust your system design, ensuring it remains efficient as conditions change.
By understanding friction loss and utilising our sizing tool, you can design more effective and cost-efficient pumping systems that maximise performance and profitability. Here are 10 tips before installing your first solar water pump.